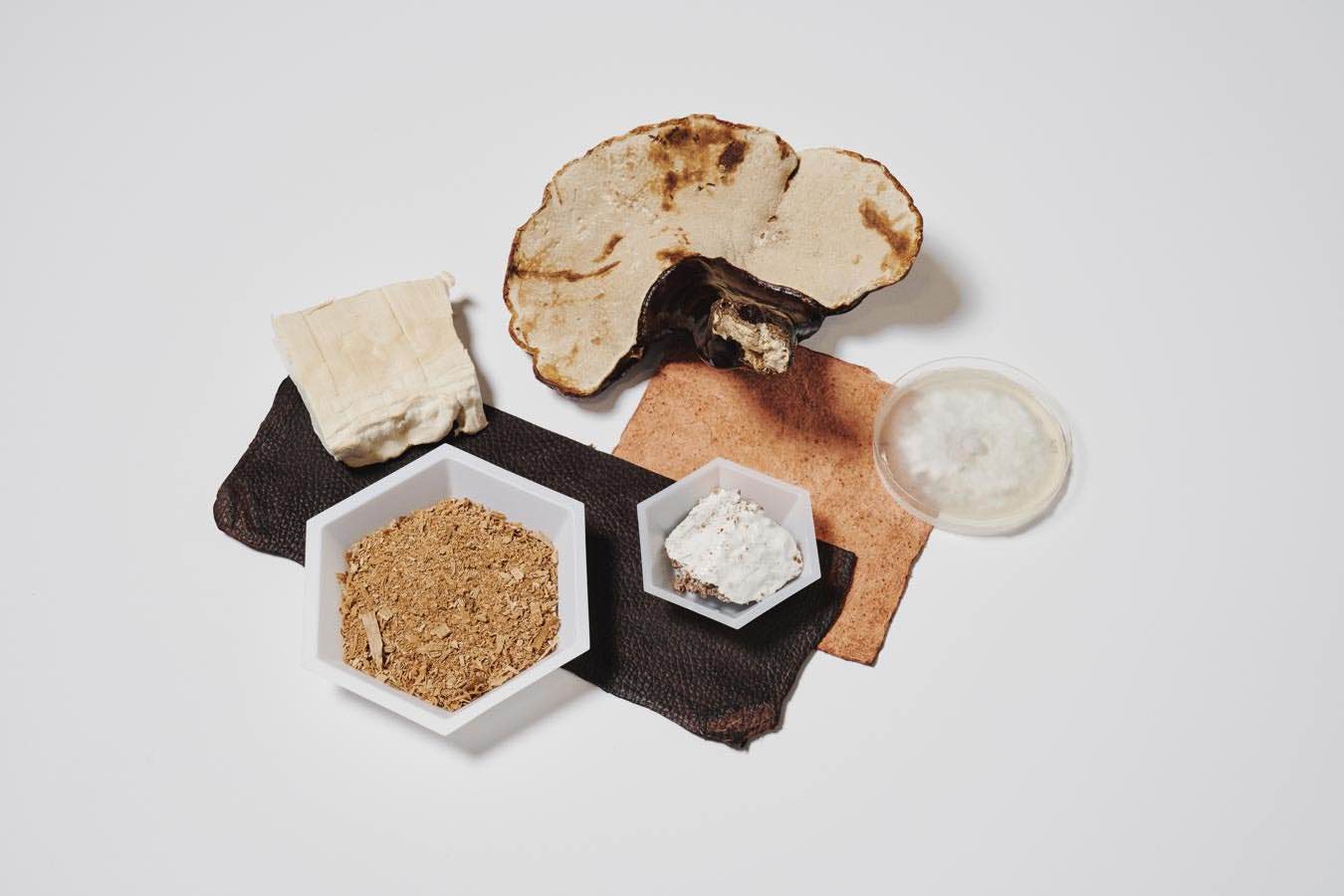
The Rise of Biotechnology in Fashion and Design
As the call to perform via a circular economic model becomes more pressing, we are moving away from synthesising some of the elements found in nature, to harnessing all its properties effectively into eco-friendly materials and fibres. Whether biodesign will be the solution to the depletion of natural resources is currently unknown, but for now, we can say that it does have the potential to alleviate our sourcing and manufacturing chemical footprint whilst eliminating waste.
Biotechnological advancements have the potential to greatly improve the overuse of land, water and environmental degradation overall. Reducing livestock farming, waste, and the use of toxic chemicals can lead to significant cuts in our global carbon footprint. Although the possibility of relying on biotechnological manufacturing at a large scale has not been assessed yet. Nor the environmental and moral repercussions of this, it is fundamental to spark discussions on how to move towards a circular economy; contemplating alternatives that allow us to live with limited natural resources whilst addressing climate change.
Bioneer—biological pioneer—was a term coined in the early nineties, when rising environmental concerns spiked. The coinage has been widely used, from ecological innovations to biotechnology—including genetic engineering. Nowadays, the focus has shifted to the development of lab-grown, biodegradable materials mainly used in fashion, design and architecture. This new approach to manufacturing goes beyond engineering sophisticated materials, for they are not only sustainable and biodegradable, but they also avoid toxicity and residual waste
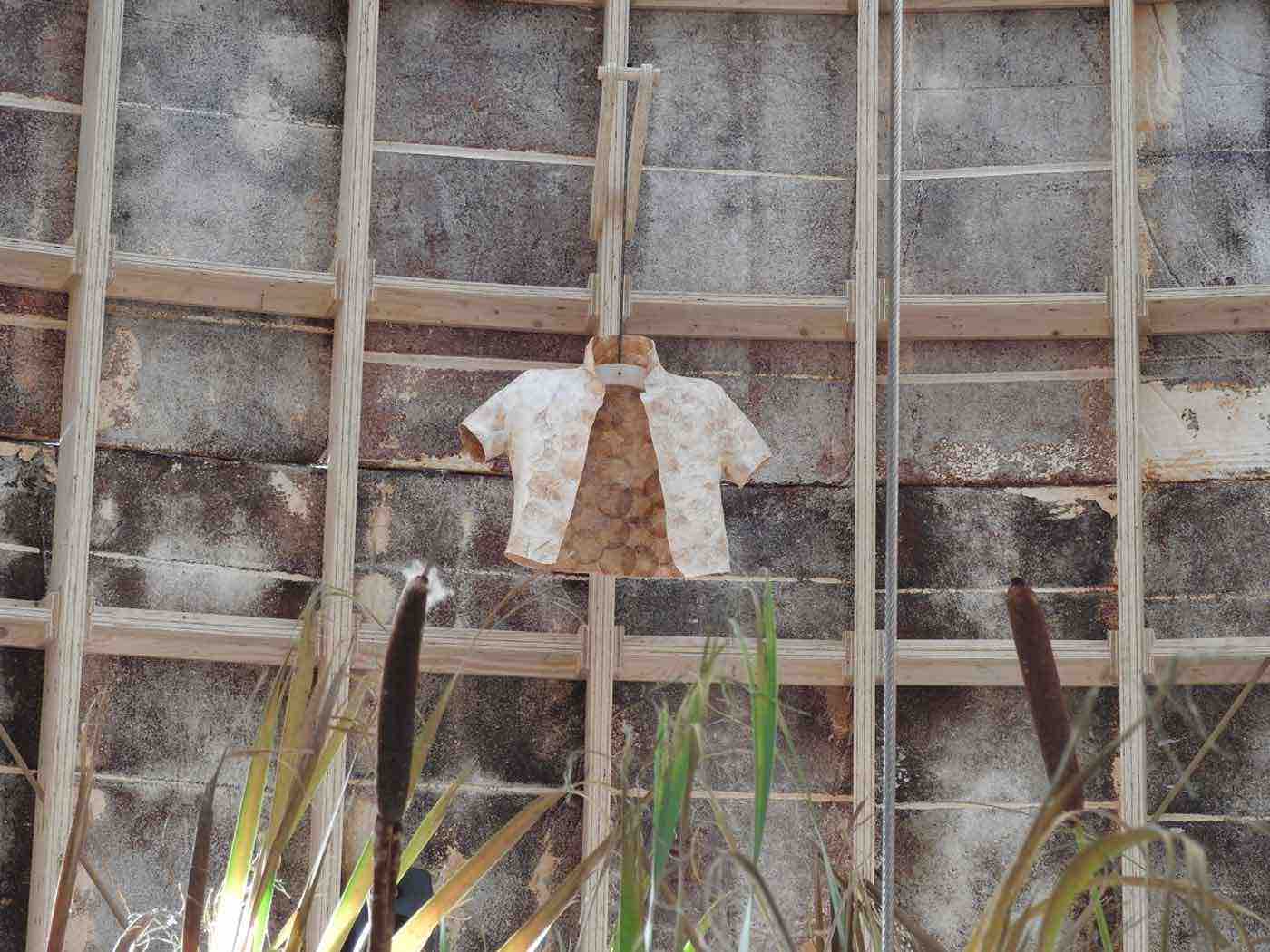
Following this thread, bioneer, then, stands for a community of biologists, material scientists and engineers who employ bacteria, fungi, algae, fermented tea, yeast, and other microorganisms, to produce garments, packagings and elements of interior design. As odd and distorted as it may sound, bioneers are dedicated, in other words, to growing clothes, boxes, textures and furniture. The idea of growing fabrics was first introduced by textile designer Suzanne Lee, a visioner of the sustainable fashion industry, in 2003. Back in the days, Lee and materials scientist David Hepworth monopolised their gardens and bathrooms to ferment bacteria. Ever since then, the Central Saint Martins graduate has been leading a new era in bioproduction, exploring ways to create animal-like materials.
Using the same ingredients to brew kombucha—such as sugar, apple cider vinegar and green tea—Suzanne Lee brought to life garments made with bacterial cellulose. Endless experiments with fermentation bore fruit: a material similar to leather that can be ditched in the composting bin since it’s both biodegradable and compostable. “You can throw it away like you would your vegetable peelings” concludes Suzanne Lee during the Wearable Futureconference held in December, 2013. Earlier this year, Luxiders spoke with Paula Ulargui on her project that interweaves plants into organic fabrics. The final product is different: Lee grows fabrics and Ulargui grows floral over-layers, but all in all, the two of them merge biology into fashion.
You are currently viewing a placeholder content from Default. To access the actual content, click the button below. Please note that doing so will share data with third-party providers.
More Information
Suzanne Lee, the head of the world’s first biodesign consultancy firm, BioCouture, and the creative director of Modern Meadow Inc—a network of developers of lab-grown materials—had it predicted: the undeniable, prosperous marriage between design, biology and technology. What comes next is a sprout of biological fabrication applied in design and architecture. The Silk Pavilion was set by the MIT Media Lab at the Massachusetts Institute of Technology in 2013. The research laboratory, led by designers, engineers, artists and scientists, created a silkworm dome using a base of robot-woven threads. The weave of delicate cocoons, technologically manipulated, was one of the first instances where digital and biological fabrication materialised at an architectural scale. Although it hasn’t been proved whether the silkworm anatomy can be incorporated into heavier architectural structures, it has been suggested that its flexibility and its rapid generation position it as a potential material.
You are currently viewing a placeholder content from Default. To access the actual content, click the button below. Please note that doing so will share data with third-party providers.
More InformationThe biotech masters Bolt Threads continued to explore bio silk for fashion purposes. In 2017, Bolt Threads launched their MicrosilkTM in collaboration with Stella McCartney. The Microsilk—engineered from DNA spider, yeast and water—is an elastic, soft, synthetic spider silk. “On a personal and professional level, partnering with Bolt Threads is so exciting, because it feels like everything is finally coming together and the dots are being connected between fashion, sustainability and tech innovation,” Stella McCartney commented on the collaboration.
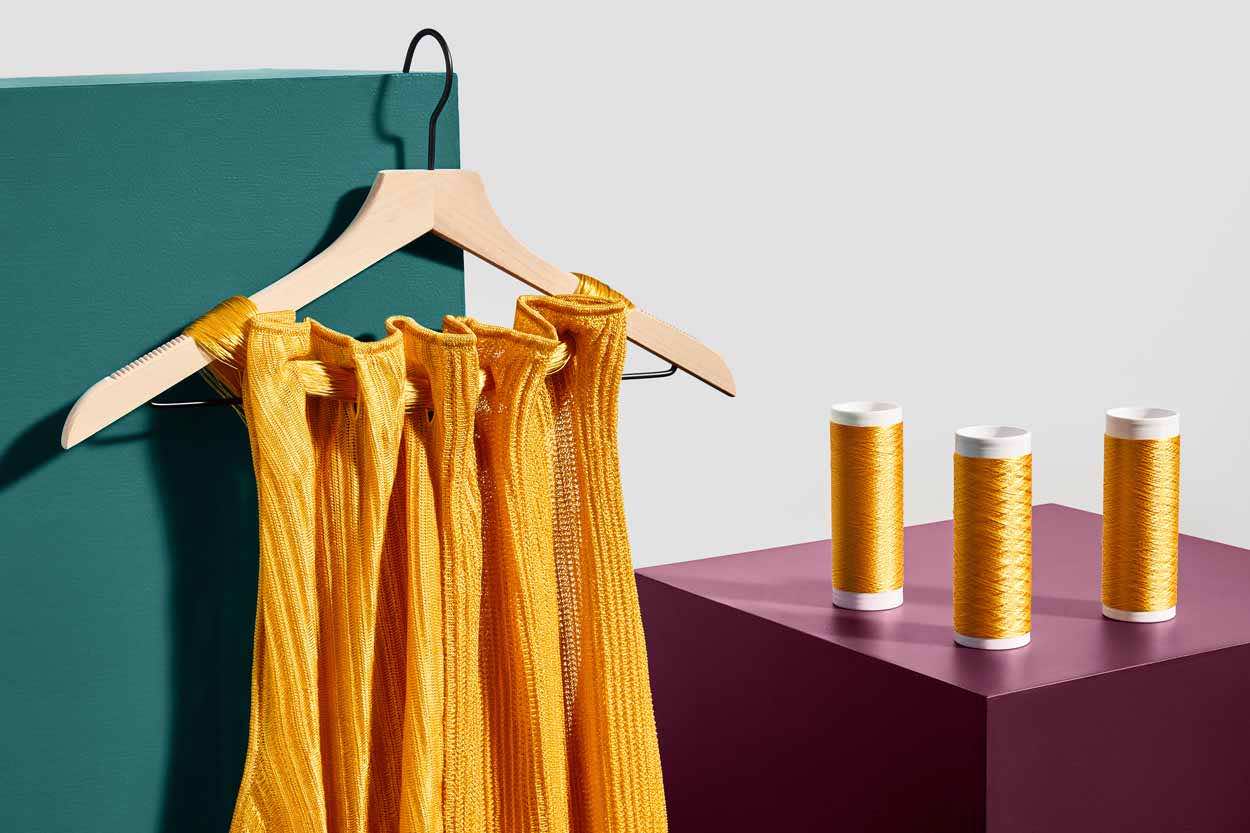
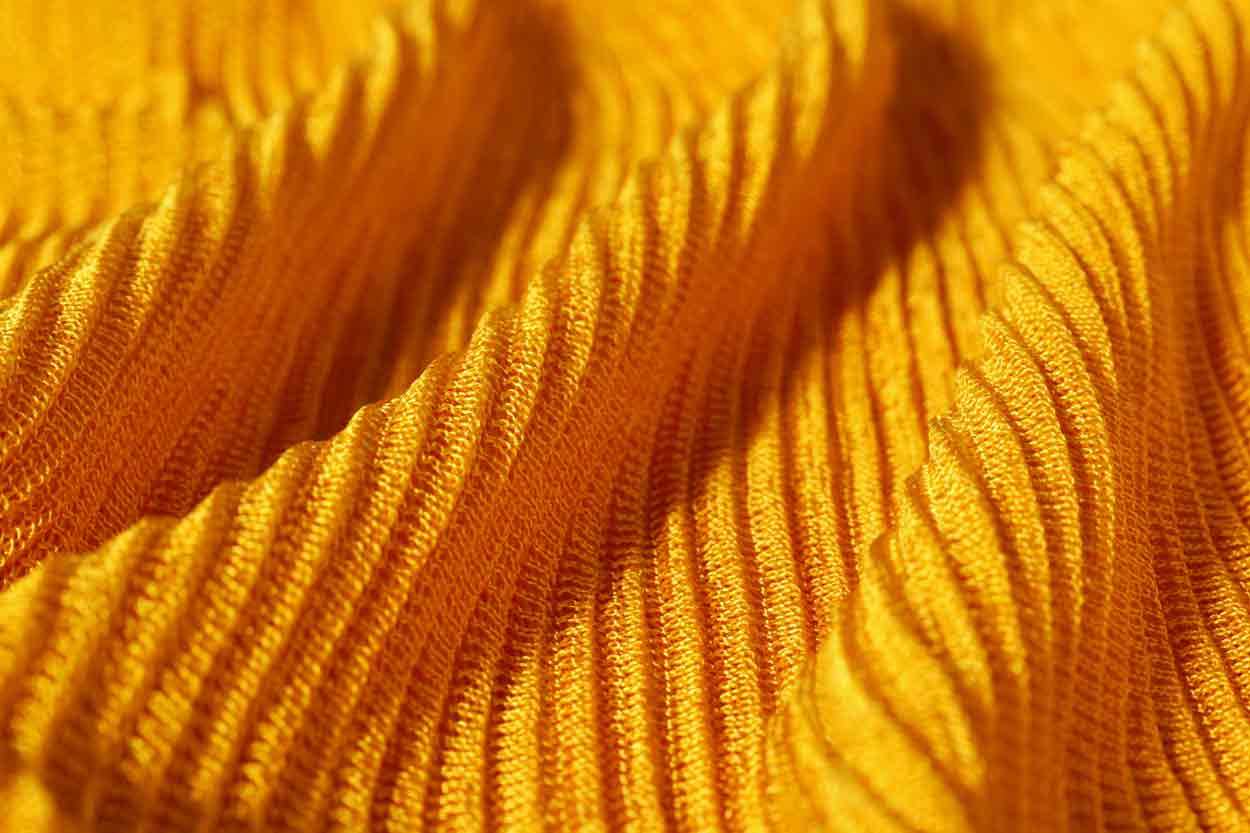
Additionally, Bolt Threads has recently licensed a vegan mushroom leather developed by the American company Ecovative Design; having applied it in partnership with Patagonia and Stella McCartney. The MyloTM is a supple leather-like material made with mycelium—which is the bacterial roots of mushrooms. The mycelium is grown and monitored in laboratories, meaning that the sourcing and production of the leather avoids livestock farming, material wastes and associated greenhouse gasses, making it a practical and environmentally-friendly alternative.
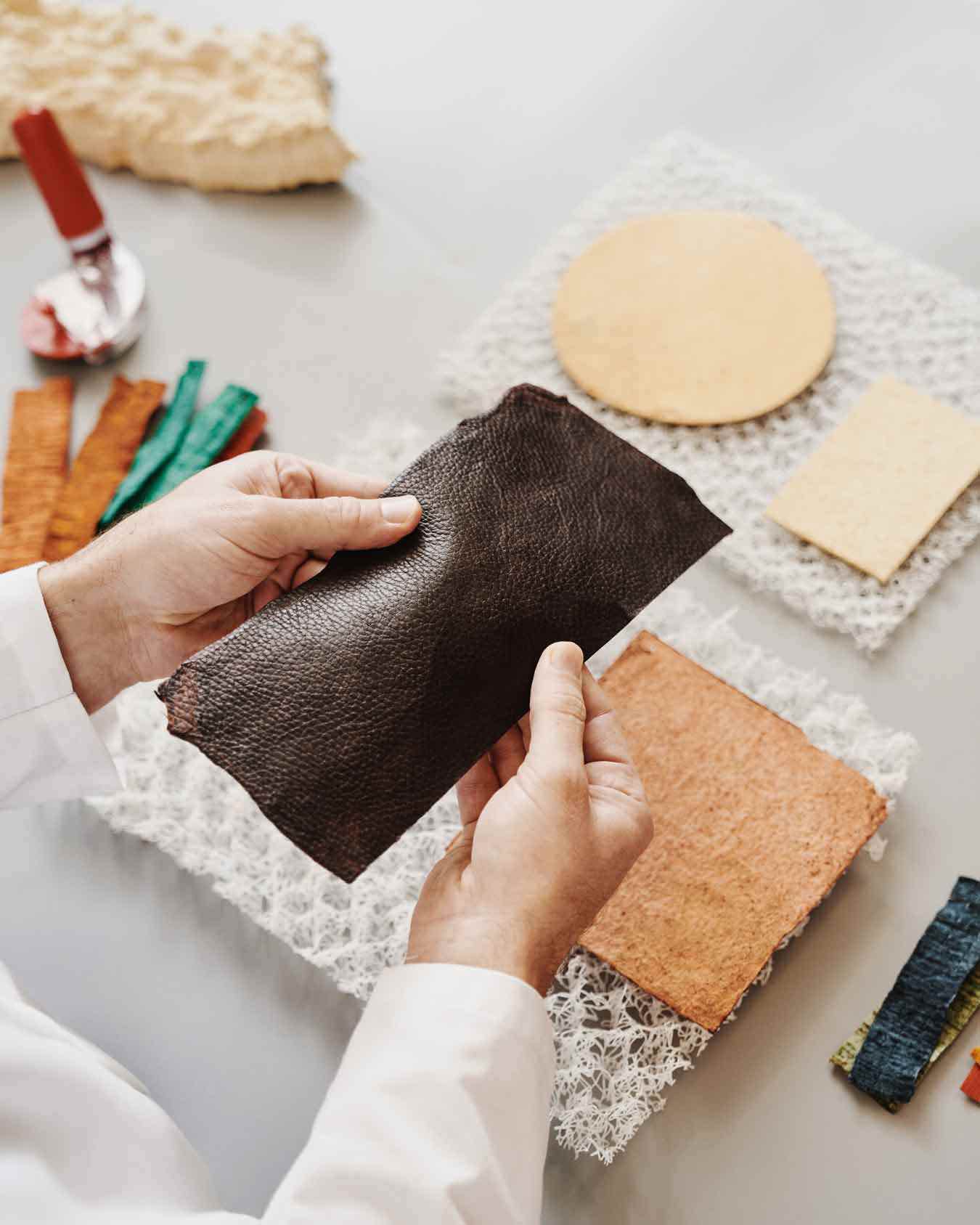
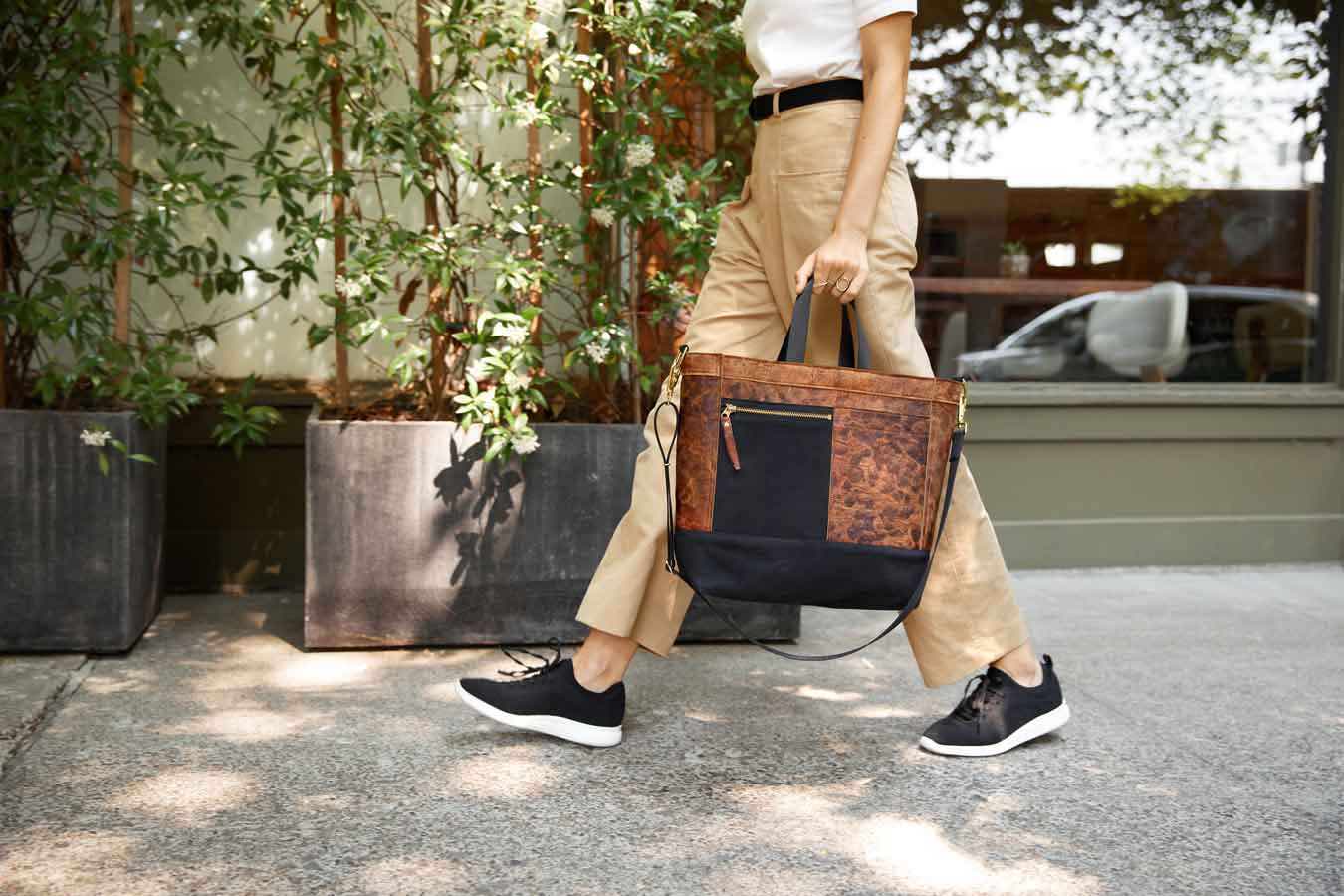
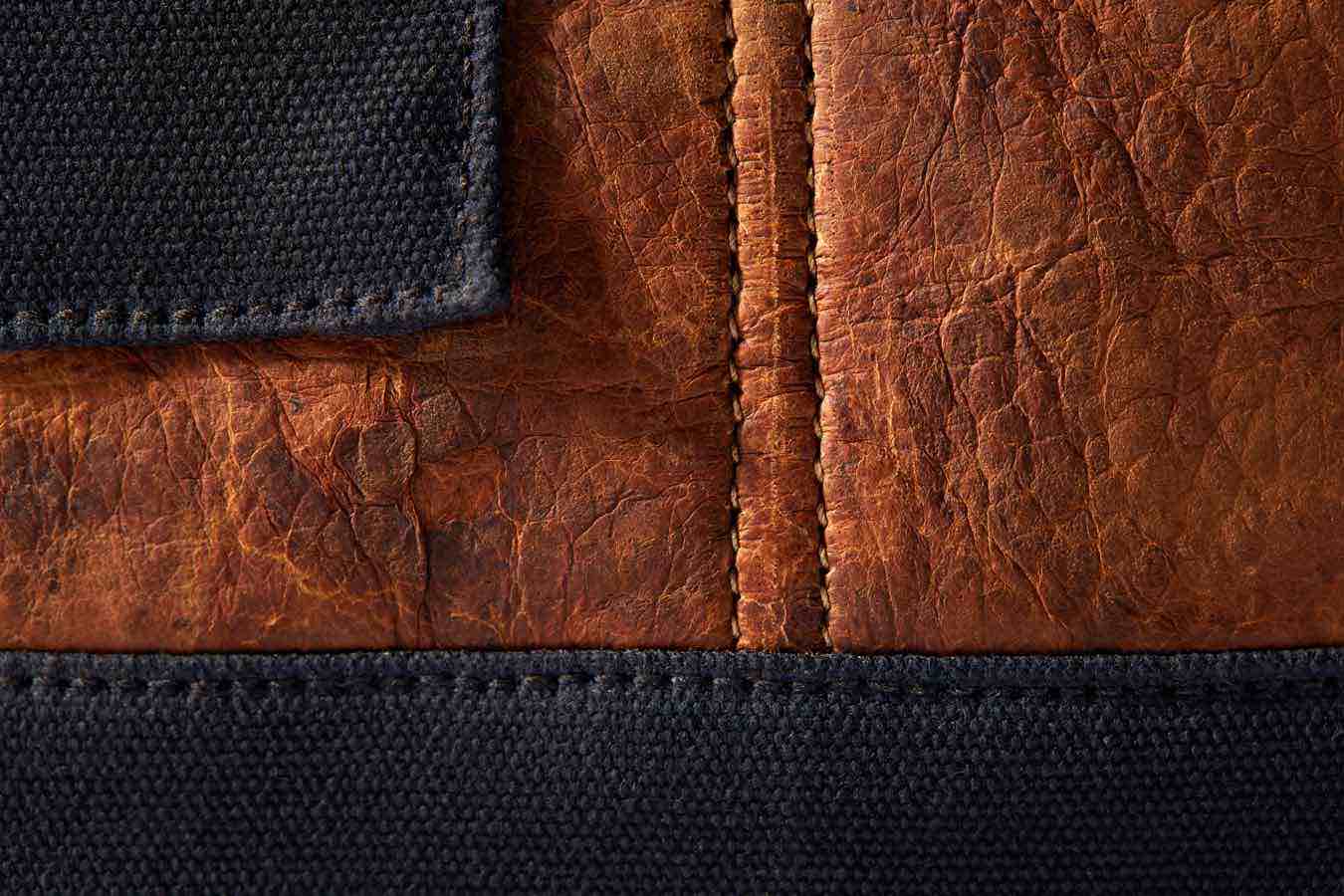
The application of mushroom-based materials are spanning the most complex and the most common structures. Grown.bio is a Dutch design studio, committed to creating sustainable materials such as packaging, insulation panels and interior design products which are not only biodegradable, but also made with negative CO2 footprint. Last year, during the Dutch Design Week, artist Pascal Leboucq partnered with Grown.Bio to set a pop-up performance space. The Growing Pavilion, supported by a timber frame, was made from growing mushroom mycelium—and other materials such as hemp and cotton— accomplishing a thoroughly biodegradable composition. The structure, explained the minds behind, was meant to inspire designers to adopt biobased building materials parented by a circular-thinking.
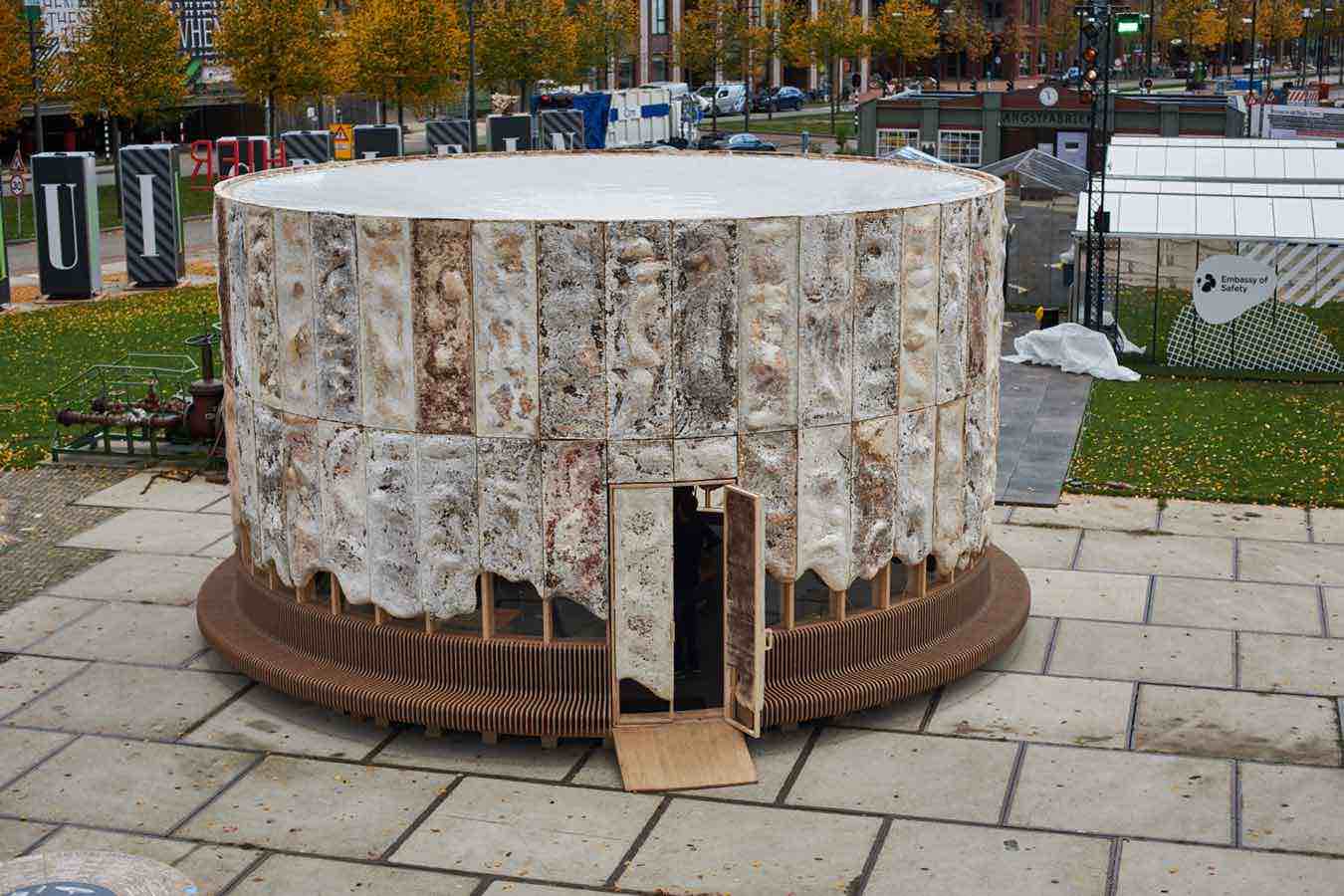
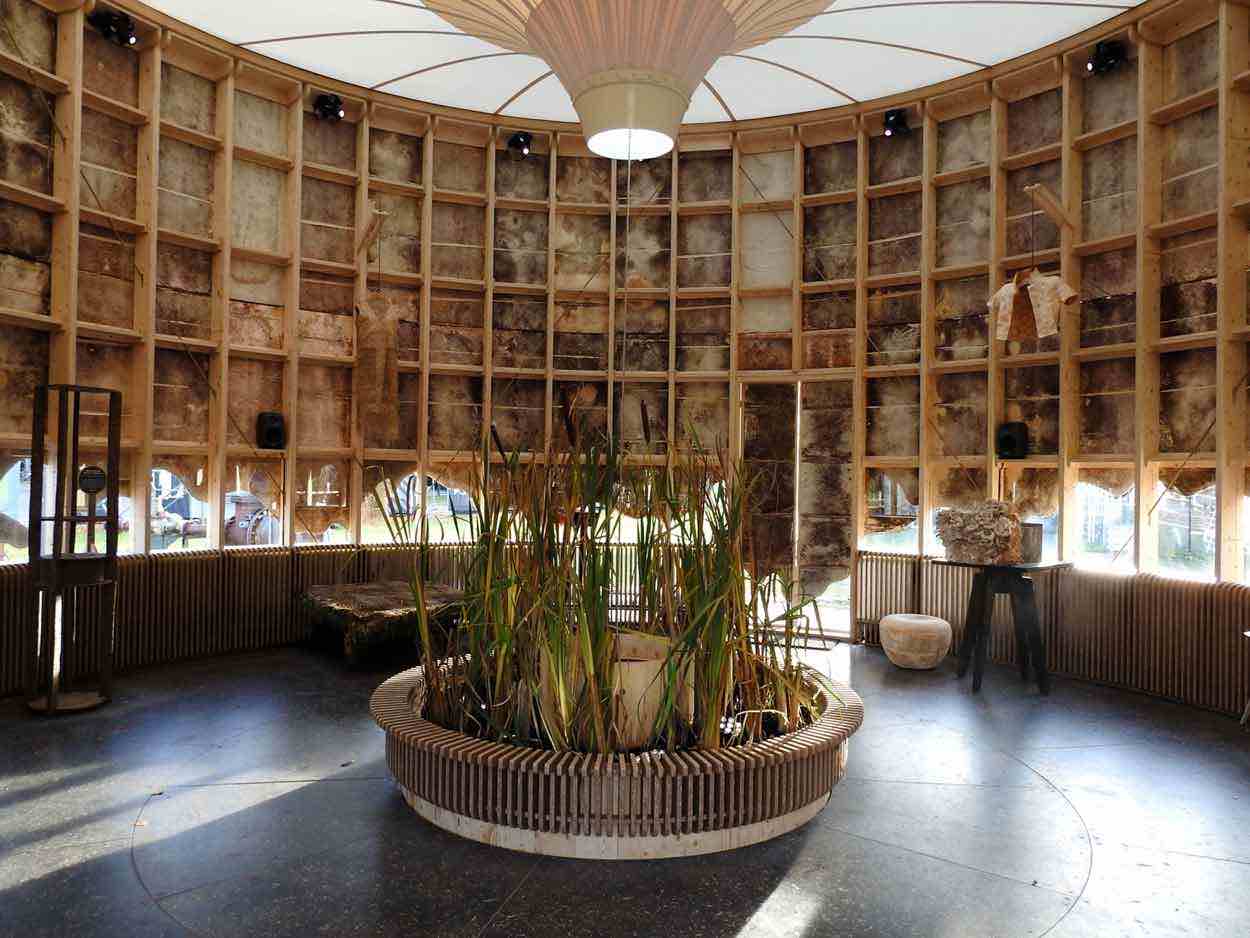
Ecovative Design and Grown.bio, besides using mycelium to create mushroom leather, packaging and insulation panels, have successfully extended the application of mycelium to furniture too, proving the infinite properties and resilience of fungus. Nowadays, Ecovative is working on developing vegetarian bacon by growing fungus in a vat, a process initiated by the British meat substitute leader, Quorn. Biodesign is on the frontline of innovation. Giants and rising designers are increasingly shifting their efforts to closing the loop between sourcing, manufacturing and consuming. Last year, graduating product design Holly Grounds invented a Dissolvable Noodle Pack. The wrapping package, containing flavourings and spices, dissolves in contact with boiling water, eliminating waste of single-use plastic. Graduating designers are acknowledging the wonders of nature and its precarious state, and are devising formulas to heal our relation to it. The Dissolvable Noodle Pack, once more, forecasts the future of our economy: a circular model accomplished by the marriage of design, biology and technology.
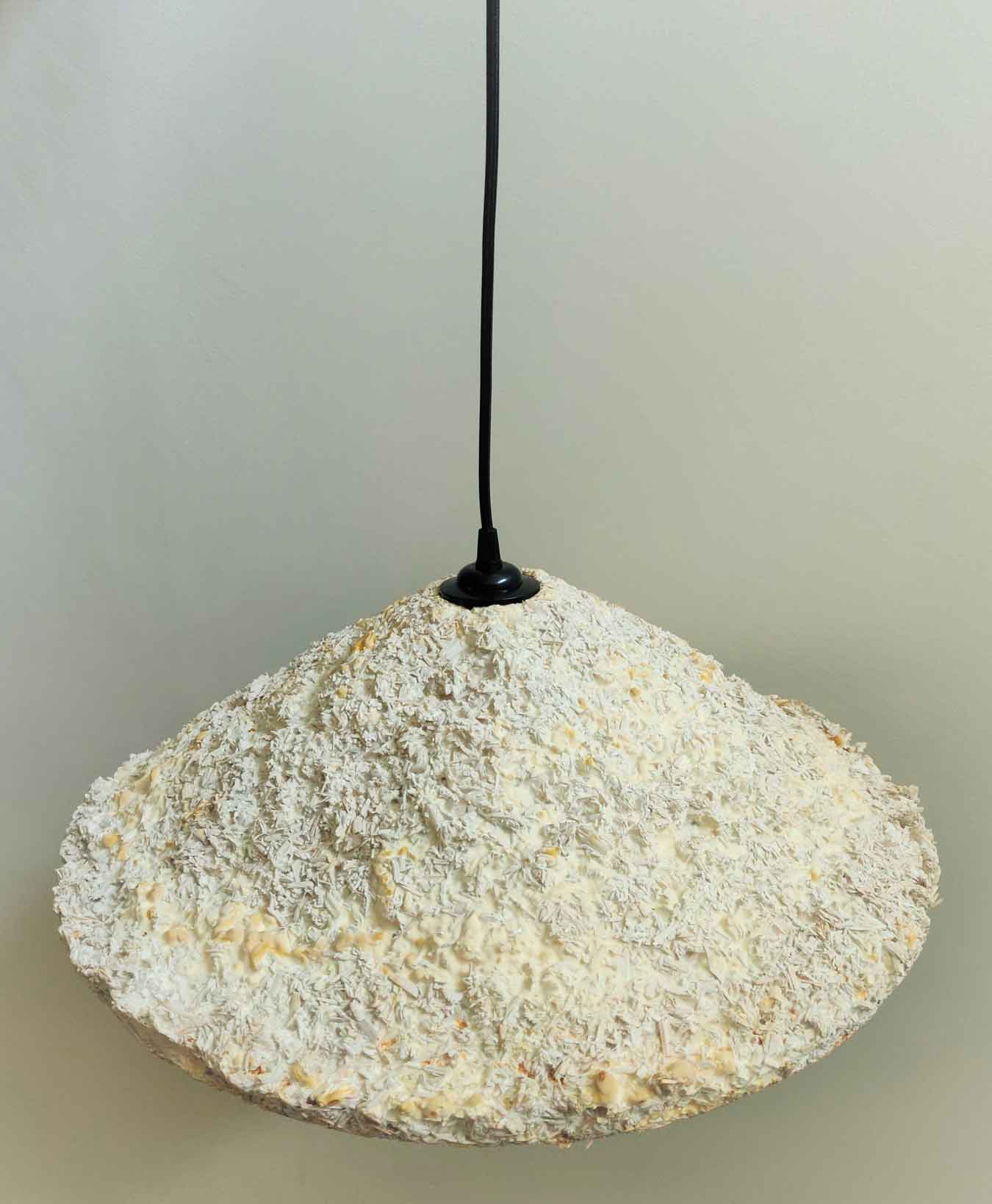